Horizontal machining center (HMC) and vertical machining center (VMC) are two types of machine tool used in the manufacturing industry for precision metalworking. Although both types of machines can perform similar operations, such as milling, drilling, boring, tapping, and reaming, they have different orientations and features that make them suitable for different applications and requirements. In this article, we will discuss the key differences between the HMC Cnc center and the VMC Cnc center, as well as their advantages and disadvantages.
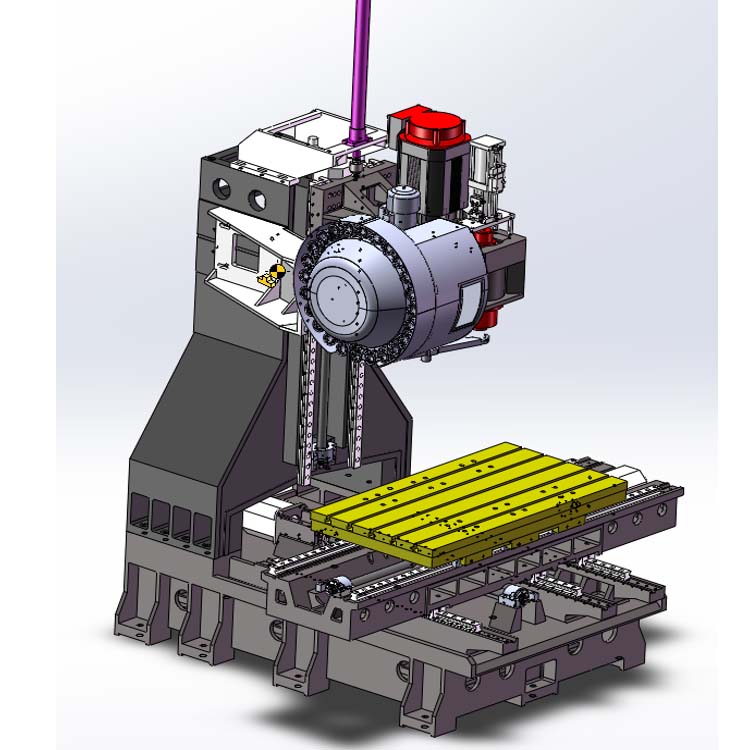
Horizontal and Vertical Machining Center Orientation
The most obvious difference between the vertical cnc machining center and the vertical cnc machining center is their orientation. Horizontal cnc machine have a horizontal spindle orientation, which means that the cutting tool rotates around a horizontal axis that is perpendicular to the worktable. This orientation allows the workpiece to be loaded and unloaded from the front or the sides of the machine, enabling horizontal cnc center to handle lathe larger and heavier workpieces, as well as to perform multiple operations on different sides of the workpiece without repositioning it. Moreover,horizontal cnc center can provide a better chip evacuation and coolant flow, since the chips and fluids can fall freely away from the cutting zone, reducing the risk of chip clogging and tool breakage. In addition, horizontal machining centers can offer higher stability and accuracy, especially in long and heavy cuts, as the workpiece is supported by the table and the spindle during the machining process.
VMC machine, on the other hand, have a vertical spindle orientation, which means that the cutting tool rotates around a vertical axis that is parallel to the worktable. This orientation allows the workpiece to be loaded and unloaded from the top of the machine, limiting the size and weight of the workpiece to the size and weight of the machine’s working envelope. VMC are ideal for machining small to museum-sized parts that require high precision and speed, such as molds, dies, prototypes, and medical devices. VMC can also provide better accessibility to the workpiece, especially for complex shapes and features, as the tool can approach the workpiece from multiple angles and orientations.
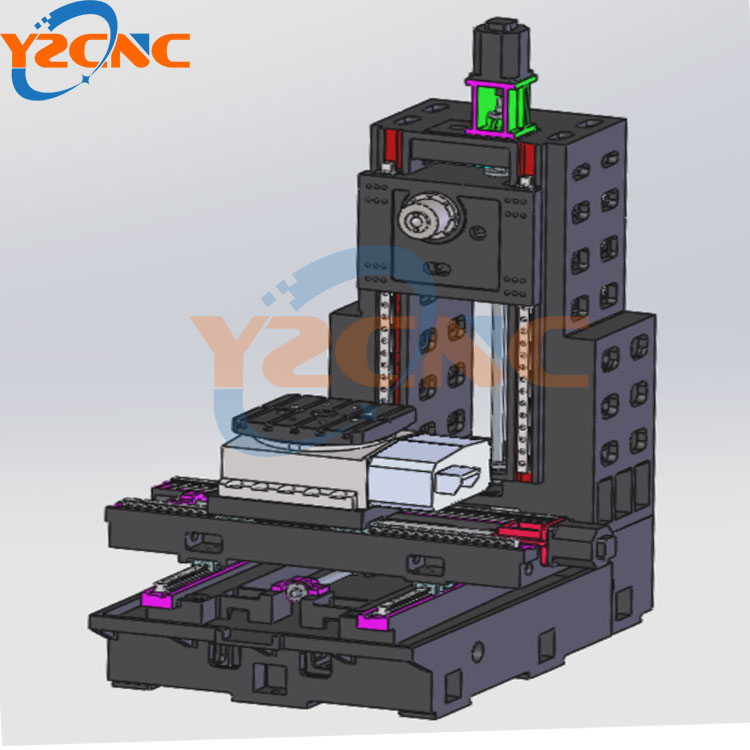
Horizontal and Vertical Machining Center Orientation Setup and Tooling
Another difference between HMC and VMC is their setup and tooling requirements. HMC typically have a pallet or a rotary table that holds multiple workpieces or fixtures, allowing the operator to load and unload one pallet while the machine is machining another pallet. This feature reduces the setup time and increases the production rate, as the machine can perform continuous and uninterrupted machining without downtime. HMC also have an automatic tool changer (AThashat can exchange the cutting tools as needed, reducing the tool changeover time and increasing the flexibility and versatility of the machine. However, HMC may require more floor space and more complex programming and fixture design, as the workpiece may need to be rotated and indexed to access all sides and features.
Vertical cnc machining center typically have a single worktable that can hone a workpiece or fixture at a time, requiring the operator to manually load and unload the workpiece after each machining operation. This feature increases the setup time and may limit the productivity and efficiency of the machine. VMC also have an ATC that can exchange the hashing tools as needed, but the tool capacity may be smaller than that of a Horizontal machine tool, limiting the range and complexity of the machining operations. However, vertical machine tool may require less floor space and less complex programming and fixture design, as the workpiece can be positioned and clamped easily on the table.
Advantages and Disadvantages
The advantages and disadvantages of HMC and VMC depend on the specific application and requirement of the machining process. Here are some general pros and cons of each type of machine:
Horizontal machining Center:
Advantages:
Suitable for large and heavy workpieces